Rick needed a new handlebar lever mount for his 1914 Blackburne, but you can’t buy such things. Only one solution – make one from a lump of aluminium
PHOTOGRAPHY: RICK PARKINGTON
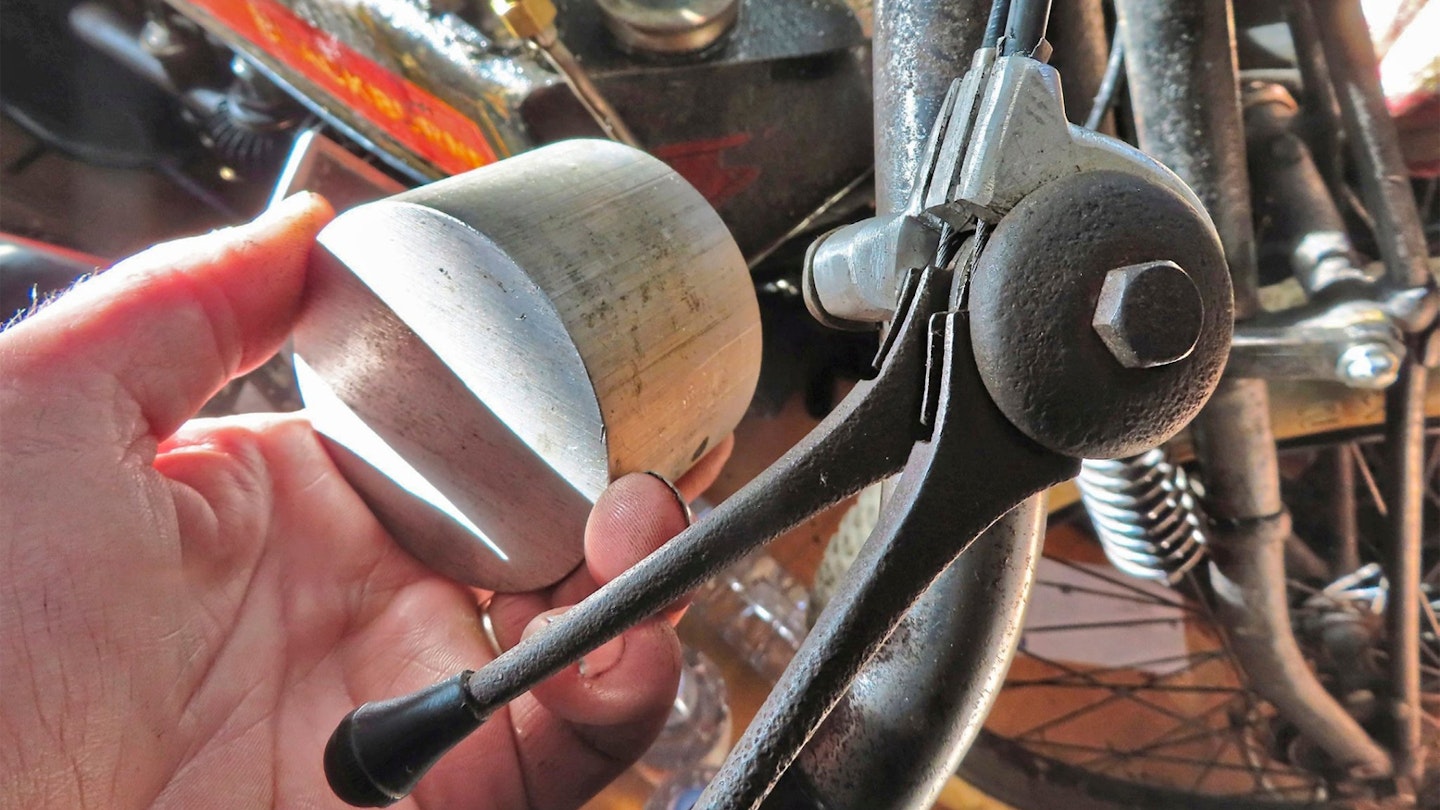
Rick Parkington: 1914 Blackburne racer
Rick’s extensive array of sheds contain lots of ancient bikes, heaps of spares and some large machine tools. With a lifetime of old bike experience and expertise, if he hasn’t got we he needs, he’ll make it himself.
‘Billet’ implies a component machined from solid, rather than turned out of foundries in thousands. It’s a popular term in customising – even if most ‘billet’ custom parts are actually turned out of Chinese CNC machine shops in thousands. But not this one.
Most of the time, replacing a part means buying one – but what do you do when you can’t get one? I had found the perfect throttle lever assembly for my ‘Scarlet Runner’ Brooklands racer – but the mounting bracket was made from Mazak, a high-zinc alloy that produces detailed castings but absorbs moisture, eventually causing corrosion and crumbling. I’ve had a few of them – but they are all 100 years old and all broken. So how about making one? Instead of casting, it seemed worth trying to machine one from solid. Luckily, I had enough broken bits to work out the shape it needed to be, so I had a go.
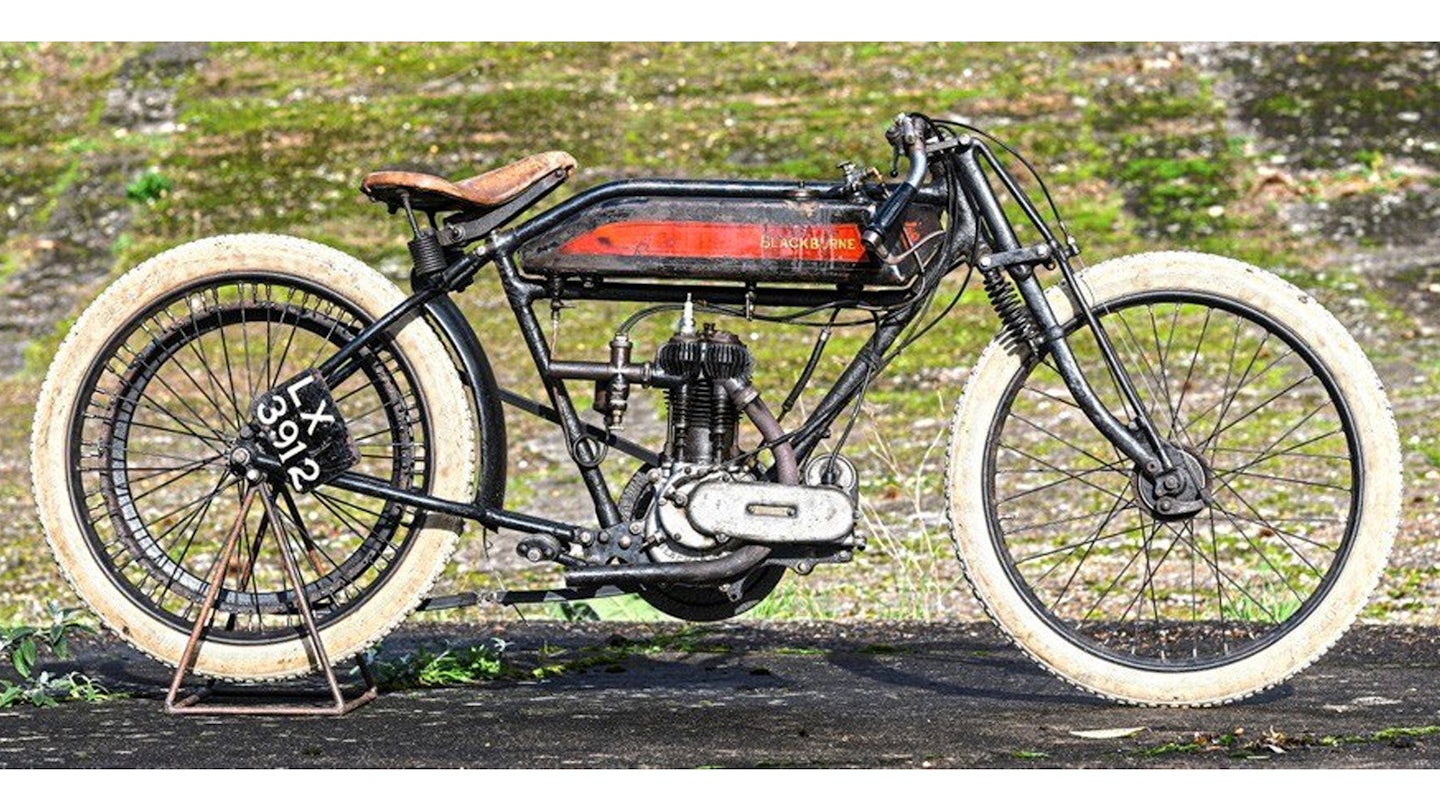
What did I learn? Well, if you have the tools, it’s not difficult – this is not precision work. The difficult bit, as so often in engineering, is holding the workpiece securely. It’s easy to paint yourself into a corner by removing metal you’ll need to grip later. Jobs like this are a series of steps; it’s an odd shape and gets odder as you go, so the trick is to think of and number all the steps, then arrange them in an order that will work. The obvious place to start is not always the best.
To read more head into stores and grab the latest issue of Classic Bike, or why not check out our subscription options so you never miss an issue!
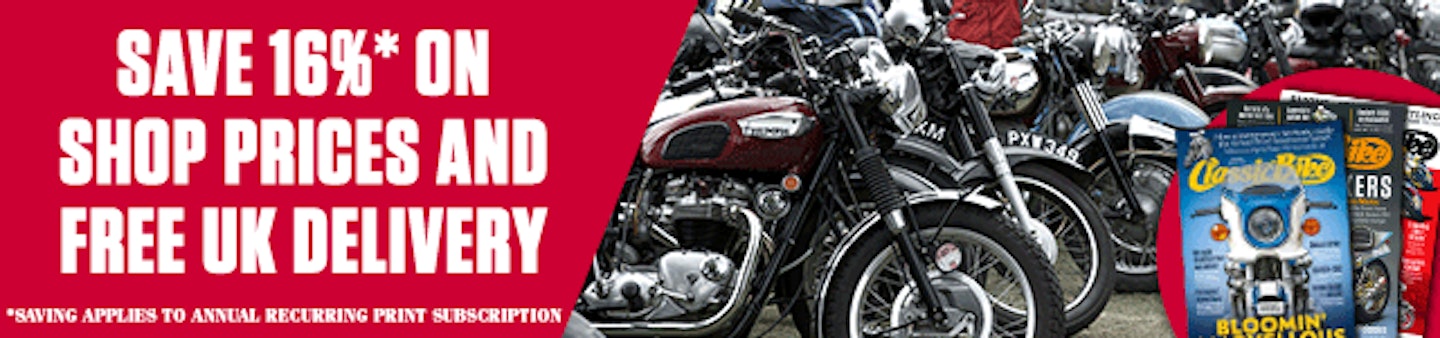